Overcoming the Elements to Build Midway Wind
The Apex Engineering and Construction team rises above the Gulf Coast’s historic rains.
Every year in November, as people across the United States are bundling up and preparing for the first snowstorms of the season, Corpus Christi enjoys relatively sunny skies and 80-degree temperatures, enticing beachgoers to the sandy shores of south Texas.
But in 2018, Mother Nature had a different plan. Autumn along the Gulf Coast brought temperatures well into the mid-90s with humidity that spiked the heat index into the triple digits. And with the heat came the rain. The sustained precipitation that began around Labor Day and lasted for weeks brought more than 40 total inches of rainfall—well over average for that time of year. Some areas received half that amount in one relentless ten-day period, creating conditions on the ground that were virtually impossible to reverse without extended, consistently dry weather.
Corpus Christi wasn’t alone; dozens of cities in the southern and eastern parts of the country shattered their rainfall records last year.
But for Apex’s team of construction engineers working on Midway Wind, located just north of Corpus Christi at an altitude only 20 feet above sea level, the deluges made for one of the most challenging and interesting construction projects in the company’s ten-year history.
“Along the coast in south Texas, the land is incredibly flat and doesn’t drain very well,” says Greg Karney, Apex’s senior project manager of construction and engineering. “That’s one of the biggest challenges we face working down here, especially with weather as severe as what we saw this past fall.”
Overcoming the extreme weather conditions that plagued the area throughout construction required flexibility and constant adjustments—on top of the expertise and precision required to smoothly and safely assemble a 162.9-megawatt wind farm.
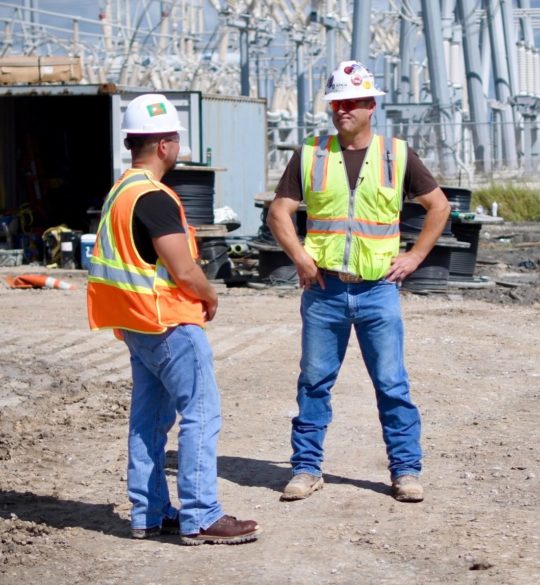
Tackling Midway’s Unique, Region-Specific Design
Even without the Gulf Coast’s extreme conditions, the crew working in San Patricio County was facing a construction process that was entirely unprecedented in the United States.
The Midway Wind project is the first U.S. install of the Siemens Gamesa 3.465-132 wind turbine. This turbine’s technology is optimized for areas like the Gulf Coast, with its medium-to-high winds, and provides the highest levels of reliability.
That level of performance comes with a 132-meter rotor diameter—one of the largest blades currently found in operations anywhere across the country.
“Larger components equal a larger turbine, which means more power production per turbine. With more power per turbine and fewer turbines per project, that results in overall cost savings for the owner of a wind farm,” explains Matt Biediger, Apex architectural and civil inspector. “The larger these components get, the more complicated some aspects of construction can be, particularly transport from point A to point B.”
Larger blades and nacelles mean both heavier and longer loads, and the team had to get even more strategic than usual in routing components from the Port of Corpus Christi to the site thirteen miles away, avoiding roads with tight turning radii and bridges that aren’t rated to hold so much weight.
“This turbine is the largest that we’ve installed to date. This required the team to work with a larger crane and account for more counterweights, but we succeeded in adapting our established work processes to maximize efficiency,” says Nathan Biediger, senior vice president of engineering and construction. “Building the Midway facility using this proven process was incredibly beneficial for productivity as well as safety and quality.”
Departure from Normal Annual Rainfall, Past Five Years Corpus Christi, Texas
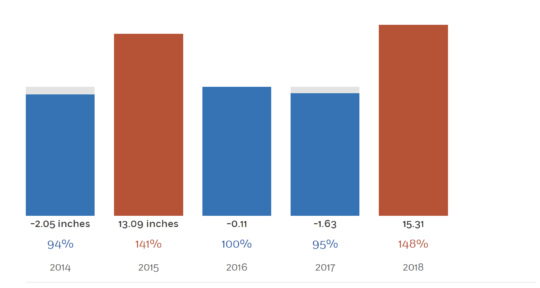
Overcoming the Elements to Prioritize Safety
For the construction crew at Midway Wind, sticking to the team’s strong fundamentals and expertise was key to reaching commercial operations successfully and safely—especially amid the unforgiving weather that plagued the site.
“Establishing a construction site is similar to creating a new organization. Even if you have all the same players involved, each time you recreate a work environment, it takes on a different form,” says Nathan Biediger. “It’s critical for us that safety is integral to that work environment, no matter who or what is involved. A strong safety performance starts with clear communication and shared expectations of zero incidents during the duration of the project.”
With hundreds of crew members on-site and over 300,000 man-hours required to fully construct the project, creating an atmosphere where safety was a core value of the work required constant reinforcement.
That emphasis on safety began well before the crew hit the ground, and in fact, even before the construction contractor was selected.
“Safety is a critical part of our selection process,” says Charles Kennedy, senior director of project management. “Before a contractor can even get one of Apex’s requests for proposal, they must go through a prequalification process that involves an in-depth review of the company’s safety program and safety statistics.”
With hundreds of crew members on-site and over 300,000 man-hours required to fully construct the 47-turbine project, creating an atmosphere where safety was a core value of the work—not just a priority that could vary depending on the moment—required constant reinforcement.
“Safety is our top priority in every one of our projects,” Kennedy says. “We want everyone to go home safe at the end of the day, and throughout the construction process and into operations, that is our number one focus and goal.”
Another Gulf Coast Success Story
Today, Midway Wind’s four dozen turbines are spinning steadily in the powerful Texas breezes. Midway joins three other Apex-developed wind energy facilities in the region: Cameron, Chapman Ranch, and Patriot.
Shortly after Apex was founded in 2009, this set of coastal projects took center stage as part of the company’s long-term development strategy. These facilities, which benefit from an impressive wind resource generated by temperature variations along the coast, were fundamental to establishing Apex’s large and diverse portfolio of assets. In a single decade, Apex has successfully originated four projects along the Gulf Coast, and land for renewable energy development in the region is now a scarce commodity.
But with the strengths of these projects came trials. Wind facilities along the coast can be difficult to develop and construct—oftentimes because of the extreme weather, which is both a blessing and a curse in this industry and the reason these projects are so remarkable. And Midway—with its unworn technology, the atypical means of assembly required, and the rains that could have thwarted it all—now represents the apex of the company’s construction achievements.
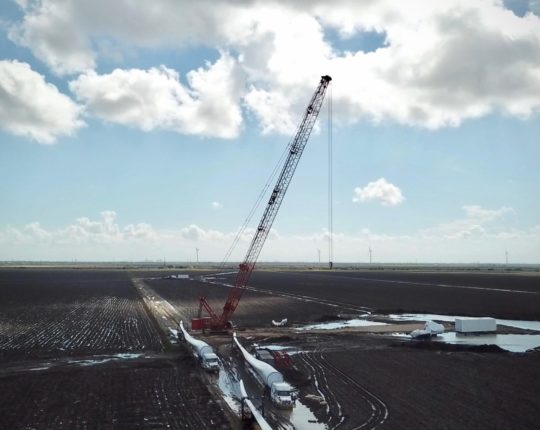